Services
The size of our team and our protracted expertise allow us to accomplish
absolutely any type of a Power plant, regardless of its height and/or complexity!

Ultrasonic Testing
Ultrasonic testing is a versatile non-destructive testing technique that uses high-frequency sound waves to detect flaws or changes in material properties. It can be used to inspect a wide range of materials, including metals, plastics, and composites, and is a popular method in industries such as aerospace, automotive, and manufacturing. Ultrasonic testing can detect internal and surface defects, making it a valuable tool for ensuring the safety and reliability of equipment and infrastructure. The technique has evolved significantly in recent years, with advances in technology enabling more accurate and efficient inspections.
Magnetic Particle Testing:
Magnetic Particle Testing is an effective and widely used NDT technique that involves inducing a magnetic field into a ferromagnetic material and applying magnetic particles to the surface. The particles will accumulate at areas where there are discontinuities, such as cracks or defects, making them easily visible to inspectors. This technique is commonly used in industries such as oil and gas, manufacturing, and aerospace to detect surface and sub-surface defects in materials.


Liquid Penetrant Testing:
Liquid penetrant testing is a widely used and cost-effective NDT technique for detecting surface-breaking defects. It involves applying a liquid penetrant to the surface of a material, which penetrates into surface cracks and defects. After removing the excess penetrant, a developer is applied to the surface, which draws out the penetrant and makes the defects visible to inspectors. Liquid penetrant testing is commonly used in industries such as aerospace, automotive, and construction to detect surface cracks and other defects.
Visual Testing
Visual testing is a non-destructive testing technique that involves the inspection of materials and components using the naked eye or specialized equipment such as borescopes or fiberscopes. It is a valuable tool for detecting surface defects, cracks, corrosion, and other irregularities that can impact the safety and reliability of equipment and infrastructure. Visual testing is commonly used in industries such as manufacturing, construction, and transportation to inspect equipment and infrastructure for defects.
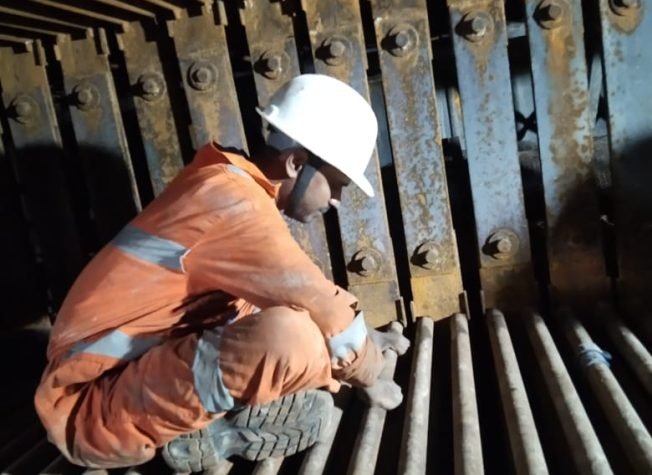

Radiographic Testing & Film Interpretation
Radiographic testing is an NDT technique that uses X-rays or gamma rays to produce an image of the internal structure of a material. The resulting image can be used to detect defects such as cracks, voids, or inclusions. Film interpretation is the process of analyzing the radiographic image to determine the presence and severity of defects. Radiographic testing is commonly used in industries such as aerospace, automotive, and nuclear power to detect internal defects in materials and components. Advances in digital radiography have led to more efficient and accurate inspections, making radiographic testing a popular NDT technique.
Ultrasonic thickness measurement (UTM)
Ultrasonic thickness measurement is a non-destructive testing technique used to determine the thickness of a material. It involves transmitting high-frequency sound waves through the material and measuring the time it takes for the sound waves to reflect back. Ultrasonic thickness measurement is commonly used in industries such as manufacturing, oil and gas, and aerospace to ensure the integrity and safety of equipment and infrastructure.

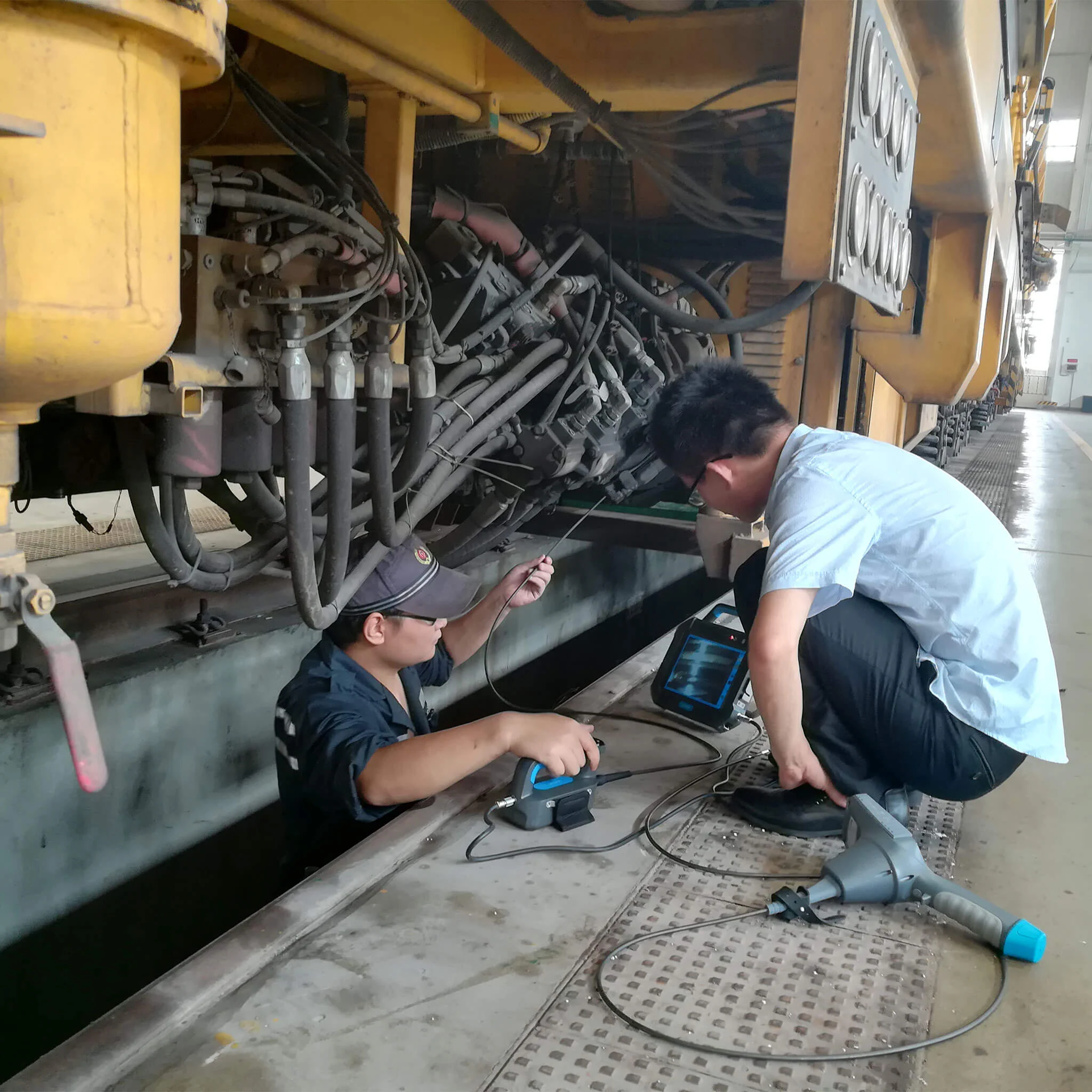
Videoscope / Borescope
Video Borescope Featured are the cube fiber based scopes for viewing, image capture and video recording for inline inspection of activity of cylinders, pressurized vessels, engines and other objects or pipe rings which cannot be inspected using conventional method.
Eddy-current testing
Eddy-current testing is a non-destructive testing technique that uses electromagnetic induction to detect flaws or changes in material properties. It is commonly used in industries such as aerospace, automotive, and manufacturing to detect cracks, corrosion, and other defects.

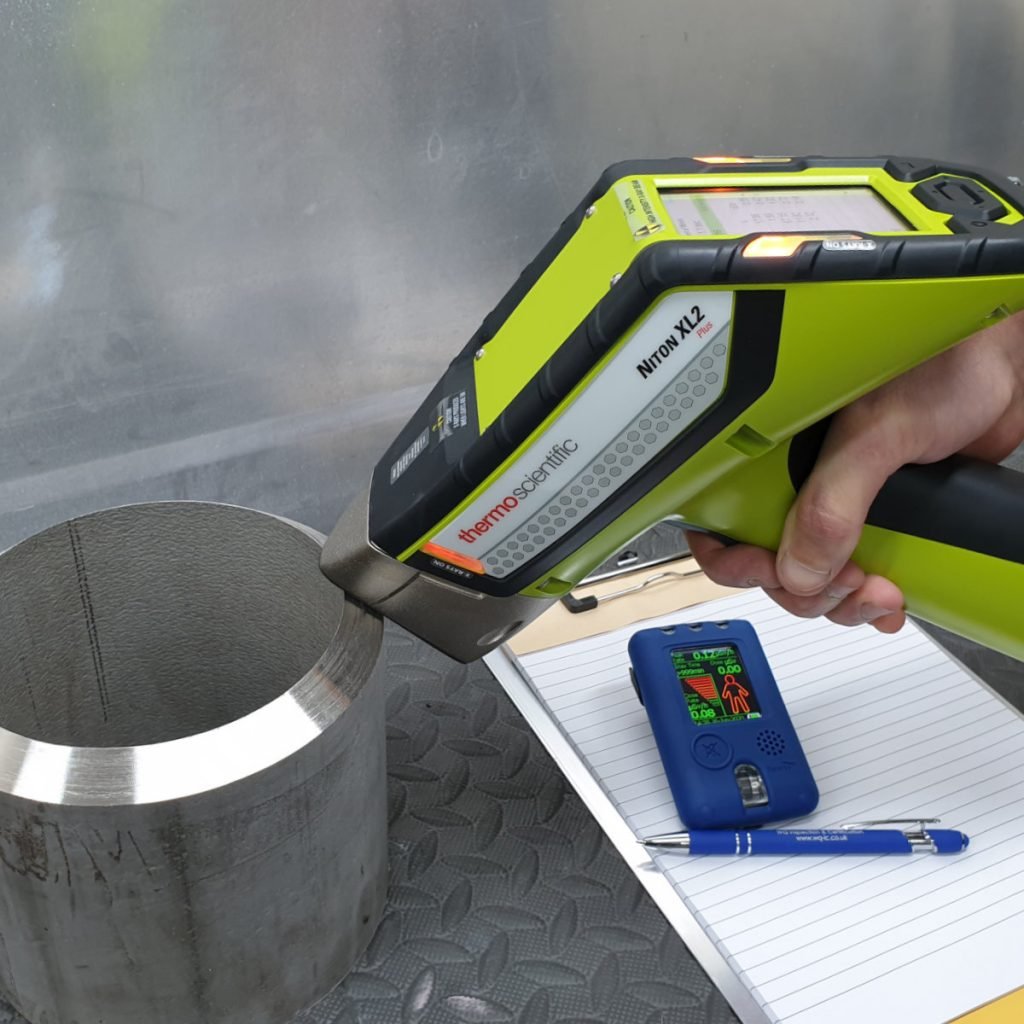
Positive material identification (PMI)
Positive material identification (PMI) is a non-destructive testing technique used to identify the composition of a material. It involves analyzing the material’s elemental composition using techniques such as X-ray fluorescence (XRF) or optical emission spectrometry (OES). PMI is commonly used in industries such as oil and gas, chemical, and manufacturing to ensure the quality and safety of materials and equipment.
Hardness measurement
Hardness measurement is a non-destructive testing technique used to determine the hardness of a material. It involves applying a force to the material and measuring the depth of the resulting indentation. Hardness measurement is commonly used in industries such as automotive, aerospace, and manufacturing to ensure the quality and durability of materials and components.
